Aluminum substrate production technology and classification
First of all, let's take a look at the production technology of aluminum substrate manufacturers:
(1) Oxidation of aluminum plate: strong degreasing (sodium hydroxide) ----- dilute nitric acid neutralization ----- roughening (honeycomb formed on the surface of aluminum plate) ----- oxidation (3UM) - ---- acid and alkali ------ sealed hole ------ baking. Each process must ensure the quality or otherwise affect the adhesion of aluminum substrates.
(2) The entire production process should not be rubbed aluminum surface, aluminum can not touch the hand, moisture and any other pollution, or affect the adhesion of aluminum substrates.
(3) aluminum substrate insulation must be kept clean, dry, small impurities affect the pressure resistance, easy to cause moisture delamination.
(4) Protective film to be affixed to the smooth, can not have voids, bubbles, or in the processing of circuit boards caused by the corrosion of aluminum syrup discoloration, black.
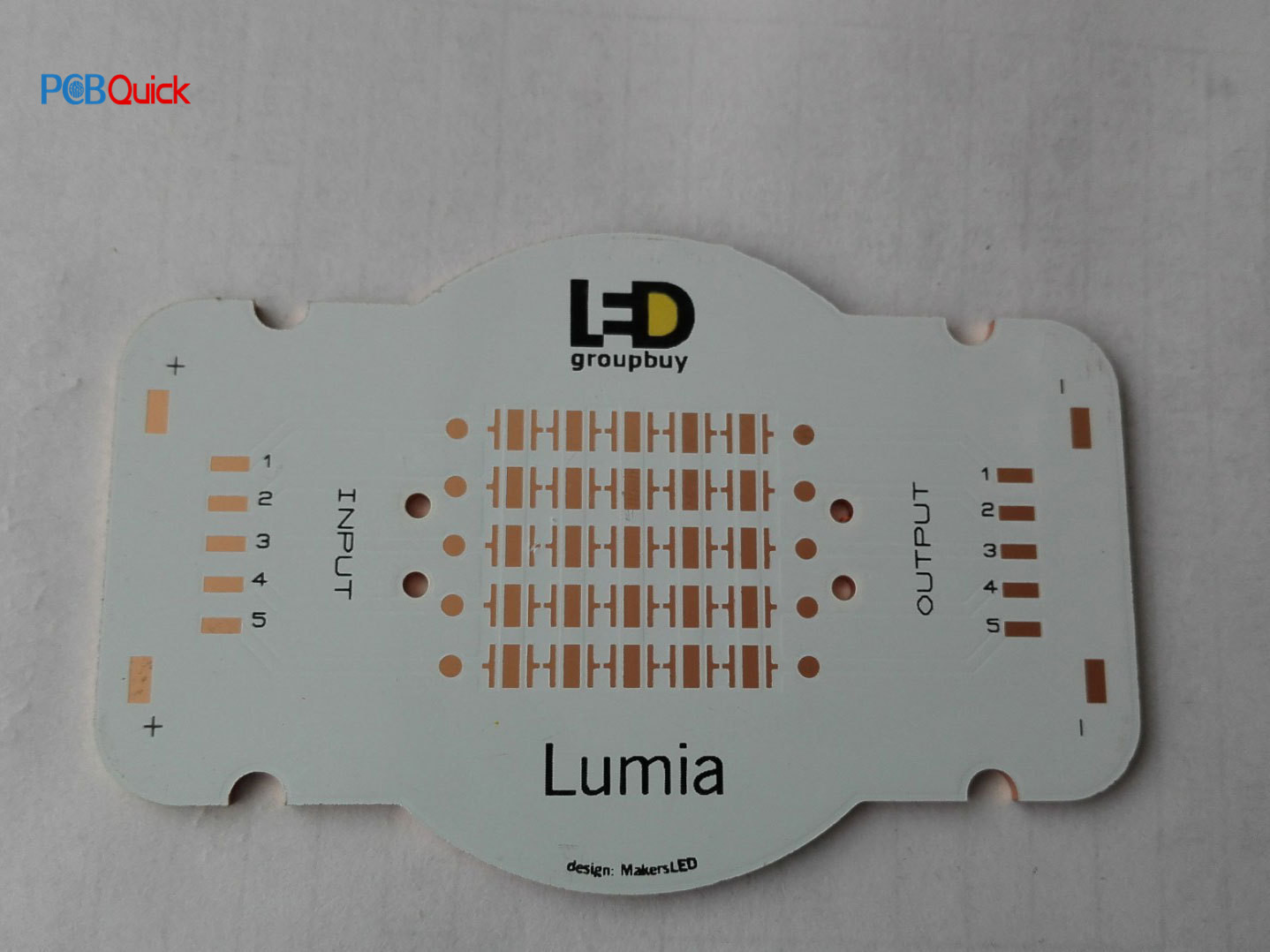
Aluminum substrate manufacturer on the line of production:
(1) Machining: The aluminium substrate can be drilled. However, no burr is allowed in the hole behind the drilled hole, which will affect the withstand voltage test. Milling the shape is very difficult. The red shape, the need to use high-level mold, mold making very skillful, as one of the difficulties of aluminum plate. After the appearance of red, the edge of a very neat, without any glitches, do not touch the edge of the solder mask. Normally use the infantry model, the hole is punched from the circuit, the shape is punched from the aluminum surface, the circuit board punches the force when it is on the shear, and so on. After the punch shape, board warpage should be less than 0.5%.
(2) the entire production process is not allowed to rub aluminum surface: aluminum surface by hand touch, or by a certain chemical products will have a surface discoloration, black, which are absolutely unacceptable, and re-polished aluminum base customers Do not receive, so the entire process does not hurt, do not touch the aluminum surface is one of the difficulties of producing aluminum. Some companies use passivation process, and some hot air leveling (spray tin) before and after the paste protective film ... ... a lot of tips, eight immortals, all supernatural powers.
(3) Over voltage test: communication power aluminum board requires 100% high voltage test, some customers require DC, some require AC, voltage requirements 1500V, 1600V, time is 5 seconds, 10 seconds, 100% PCB for testing. Dirt on the board surface, burrs on the edges of the holes and the aluminum base, jagged lines and scratches on any small insulating layer can cause high voltage test fire, leakage and breakdown. Pressure test board stratification, blistering, are rejected.
In addition, the aluminium plate is divided into the following categories:
First, a general-purpose aluminium-clad board, the insulation layer made of epoxy glass cloth adhesive sheet;
Second, high heat-based aluminium-clad laminate, the insulation layer of high thermal conductivity of epoxy resin or other resin composition;
Third, high-frequency circuit with aluminum-based CCL, insulation layer made of polyolefin resin or polyimide resin glass cloth bonding sheet.
Aluminum-based CCL and conventional FR-4 CCL is the biggest difference in heat dissipation, with a thickness of 1.5mm FR-4 CCL compared with the aluminum-based CCL, the former thermal resistance of 20 ~ 22 ℃, the latter the thermal resistance of 1.0 to 2.0 ℃, the latter is much smaller.
Aluminum substrate
Maybe it’s helpful to you:
Web link