Team building in PCBQuick LED PCB Factory
Led circuit printing board manufacturer:Team building on the front line
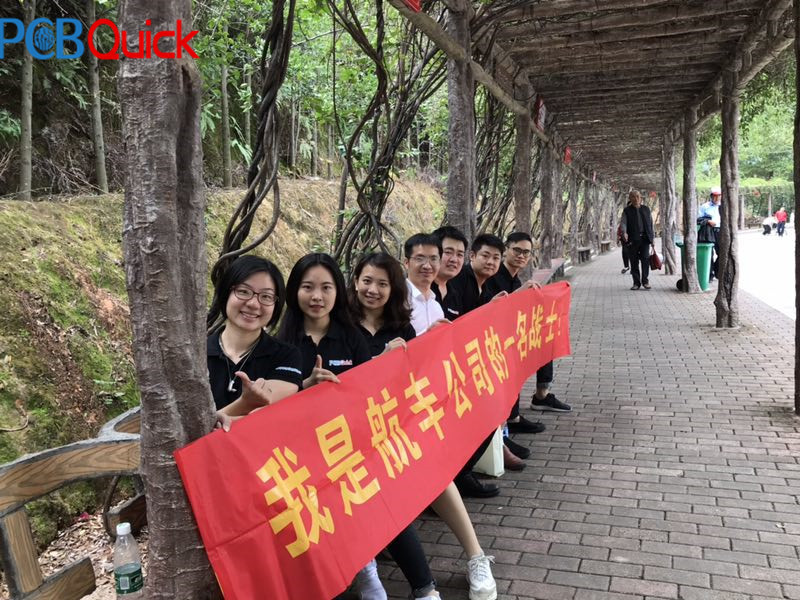
Construction of the team
The purpose of the activity: through a series of quality expansion activities, enhance employees' trust in the team and others. Cultivate the spirit of teamwork, visit the factory production process to improve professional ability, so that employees have a more positive and optimistic attitude to face the work and life.
Activity time: November 23-24
Location: In PCBQuick LED PCB Factory
Participants: all staff of KingFung technology co., LTD
Dust-free workshop
The colleagues in the factory held a simple and warm welcome ceremony for us and then started the learning journey of the factory.The first thing we did was to take a shoe cover, because most of the factory area is a dustproof workshop, wearing safety and labor protection equipment is a must.
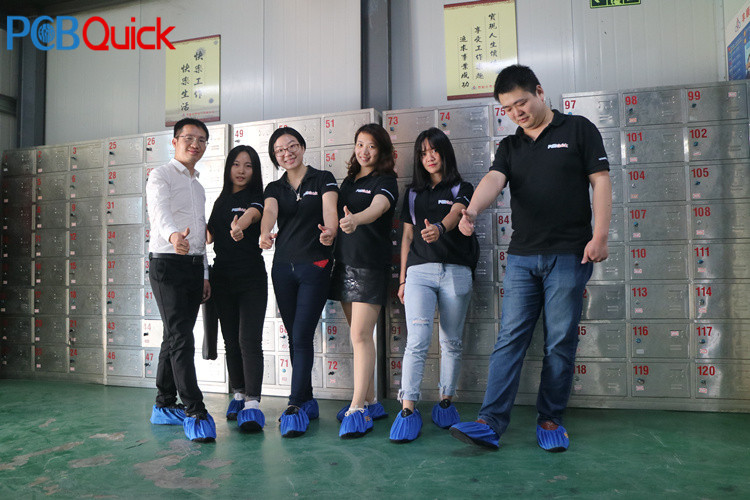
Base material & loss parts warehouse
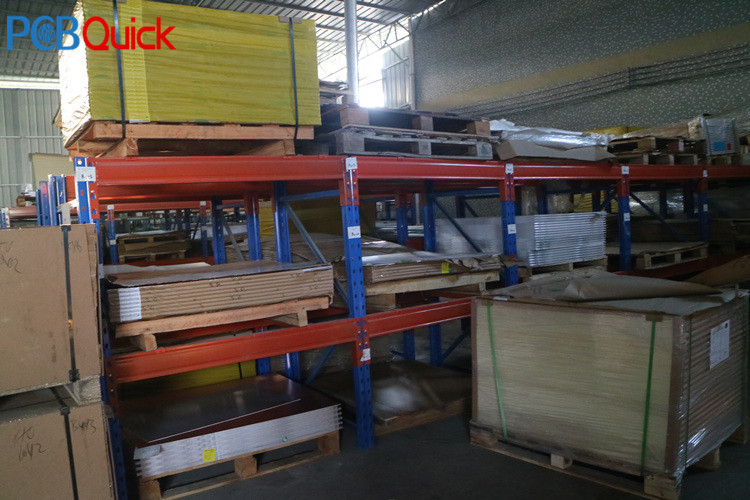
Base material storage
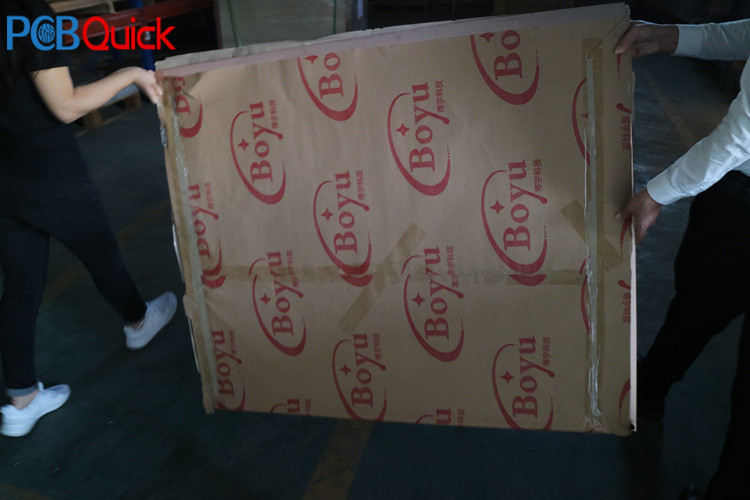
Outer packing of materials
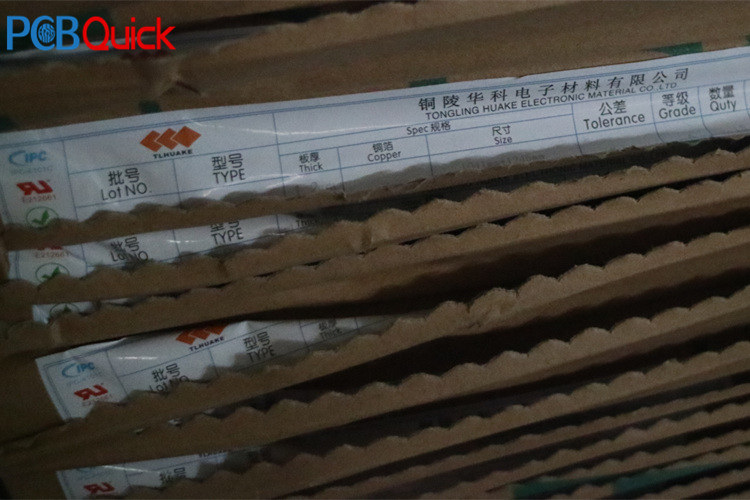
Production date and security certification
Warehousing management: collect materials according to the provisions of material acceptance; According to semi-finished products, finished products warehousing provisions point receipt and warehousing; Arrange the materials in order; Nonconforming products shall be labeled or disposed of.
Outbound management: issue materials according to the provisions of the distribution list; Strictly implement the first-in, first-out principle to deliver goods and leave the warehouse.
Storage and storage: properties of storage materials, storage requirements, can be targeted for storage, prevent goods damage, improve the quality of storage; Station tools and pallets should be properly kept and used carefully to ensure extended service life.
Account card management: establish complete material account and material card. The account will be completed on the same day. Make warehouse reports on a regular basis.
Warehouse 5S management:
SEIRI, SEITON, SEISO, SEIKETSU, SHITSUKE
Led PCB production process
Aluminum PCB Flow Chart | |||||||||||
Material Purchasing | → | IQC | → | Cutting | → | CNC Drilling | → | IPQC | → | Image Transfer pertreatment | |
↓ | |||||||||||
IPQC | ← | Etching | ← | IPQC | ← | Developing | ← | Exposure | ← | IPQC | |
↓ | |||||||||||
Solder Mask Dretreatment | → | IPQC | → | Solder Mask Printing | → | Solder Mask Baking | → | Solder Mask Exposure | → | Solder Mask Develop | |
↓ | |||||||||||
IPQC | ← | Surface Treatment | ← | Legend Curing | ← | IPQC | ← | Legend Printing | ← | IPQC | |
↓ | |||||||||||
Pouting | → | V-cut | → | Clear | → | ET-TEST | → | Final | → | Packing | |
8 IPQC(InPut Process Quality Control),guarantee product quality 、safty and reliety | |||||||||||
Material Purchasing&Cutting
Objective: to cut large copper-clad plates into the size required for production, so as to facilitate production
Process: material selection - quantity - size - cutting board
Note: determine plate type, copper thickness, plate thickness, plate longitude and latitude, avoid scratching the layout.
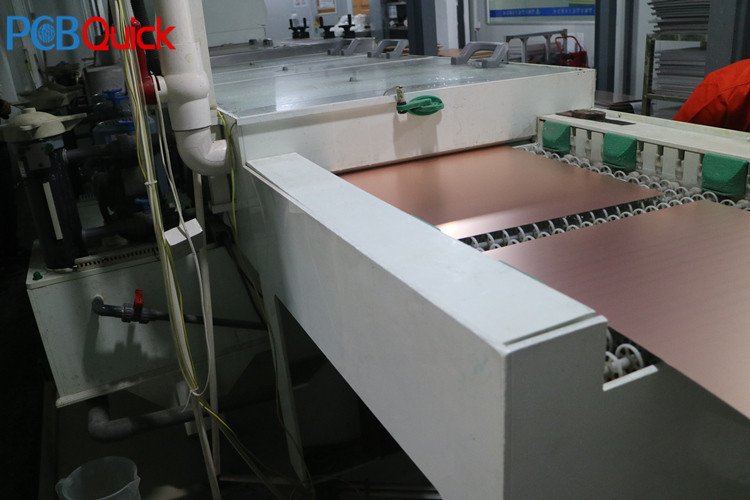
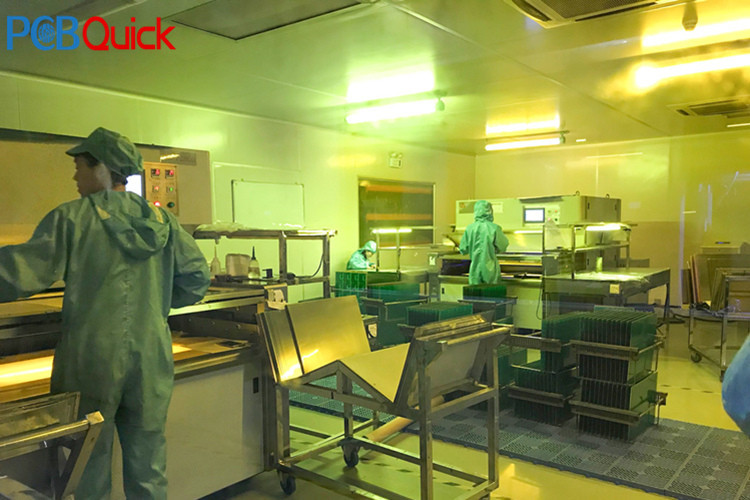
Line & soldering resistance
Process:Image Transfer Pertreatment, Exposure, Developing, Etching, Solder Mask.
Clean workshop dress code:Clothes and hats should be clean, neat and well-dressed; Girls' hair is tied up with the cap inside. Contact products must wear gloves and electrostatic rings.
Graphic cutting & Pouting
Including:Surface text, Graphic cutting, v-cut
Maximum machining size:
1500mm*600mm
The PCB circuit board is cut into small boards in the following ways: milling cutter, cutter, punching, sawing, laser cutting and so on.
Requirements: cutting edge without dust, no burrs, no deformation, will not affect the edge components.
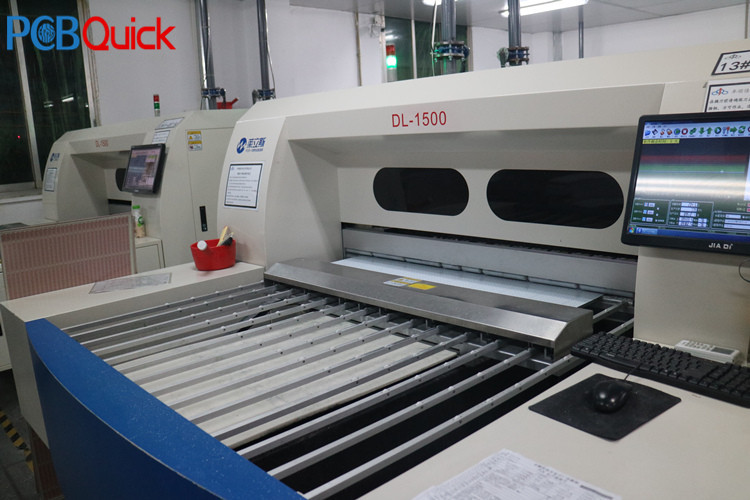
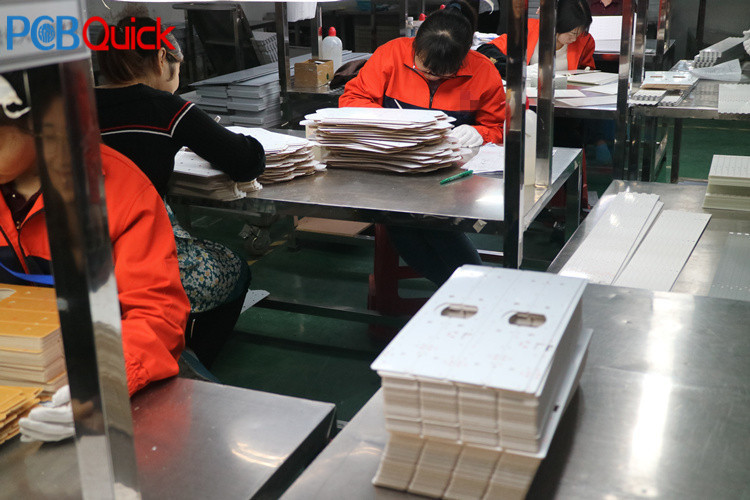
Product testing
Visual inspection: it is to point to use naked eye and use 3 times or 10 times magnifying glass to undertake examining, to local and apparent defect, need to use taller magnifying glass to do appraisal and judgement, to the quality requirement of all sorts of dimensions respect, if the measurement of line width, line distance, need to use the magnifying instrument that has mark line or scale to undertake measuring. Through hole plating part, need to be about 100 times to check the integrity of copper foil and hole wall coating.
Judgment criteria: purchase documents, product master drawings, customer requirements, general international standards (IPC).
PCBQuick aluminum PCB factory, specializing in the production of LED lighting PCB, TV backlight PCB products; We are equipped with 1500mm long exposure machine, testing machine, automatic v-cut, automatic shooting machine and pressure plate warping equipment, which can complete 1500mm long LED PCB Board without warping at one time. Aluminium PCB board to provide a professional pressure test, ensure that all Aluminium PCB board after completion of the pressure and thermal conductivity requirements. The latest v-cut section technology, a good solution to the customer break apart the line burr problem.
This new process learning and training in the factory has improved the professional knowledge of the entire foreign trade team, which can better provide our customers with professional answers to LED PCB products, so as to improve customer experience service. After the training, our team carried out a mountaineering group building activity to enhance the degree of cooperation among colleagues and improve the spirit of teamwork.
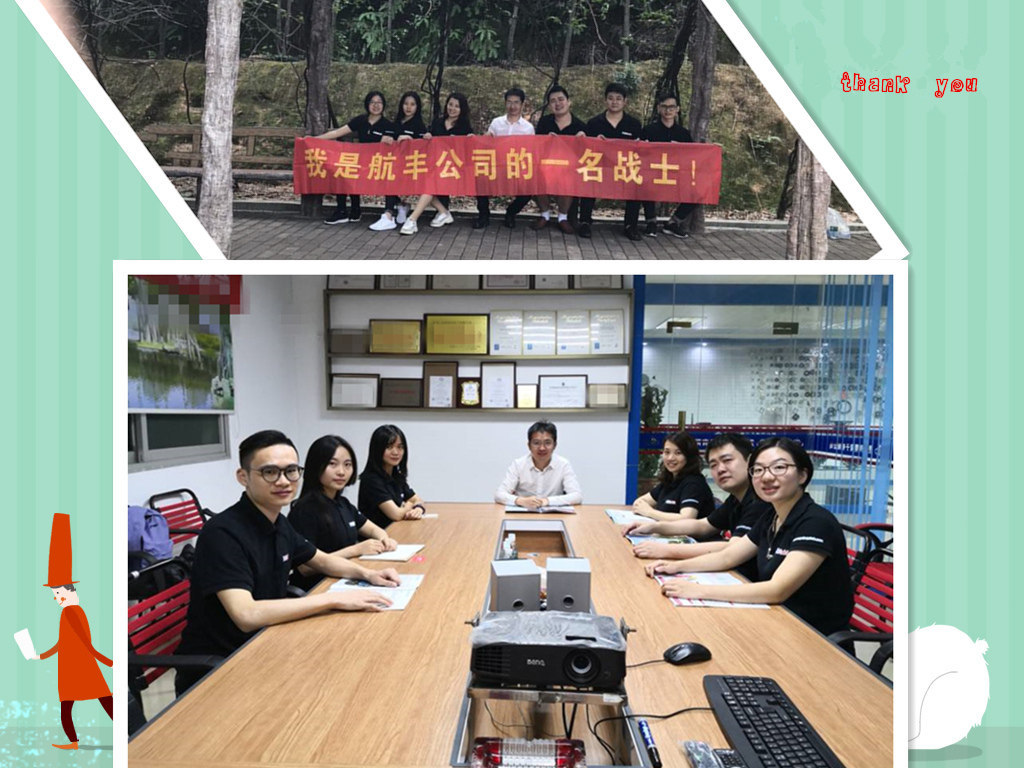