The Methods and Precautions of Shearing and Sawing Printed Circuit Boards
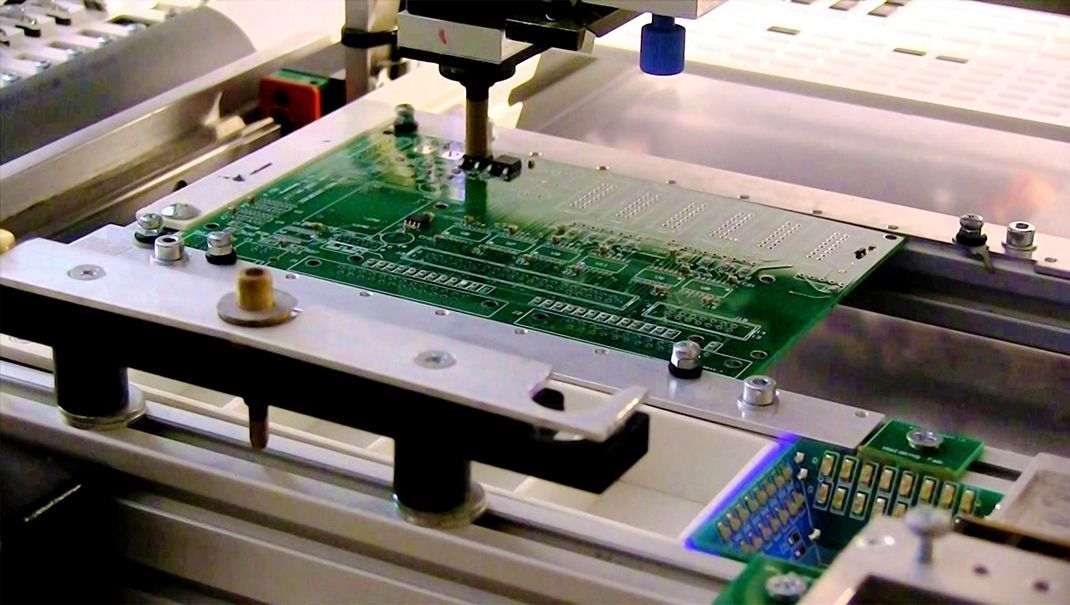
The circuit board needs to be cut during the processing because the circuit board model and use are different, and the cutting shape of the circuit board is also different. The following mainly introduces the shearing and sawing methods of printed circuit boards.
Shearing
Shearing is the first step in the mechanical operation of the printed circuit board, and the rough shape and outline can be given by shearing. The basic cutting method is suitable for all kinds of substrates, and the thickness is usually no more than 2mm. When the cut board exceeds 2mm, the cut edges will appear rough and irregular. Therefore, this method is generally not used.
The shearing of the laminate can be a manual operation or electromechanical operation, no matter which method has common characteristics in operation. The shearing machine usually has a set of adjustable cutting blades, the blades of which are rectangular, the blade at the bottom has an adjustable angle of about 7°, and the cutting length can reach 1000mm.
The longitudinal angle between the two blades is usually best to choose between 1°-1.5°, the use of epoxy glass substrate can reach a maximum of 4°, the gap between the cutting edges of the two blades should be less than 0.25mm.
The angle between the two blades should be selected according to the thickness of the cutting material. The thicker the material, the greater the angle required. If the cutting angle is too large or the gap between the two blades is too wide, cracks may occur when cutting the paper substrate.
However, for epoxy glass substrates, due to the material's certain bending strength, even if no cracks appear, the board will be deformed. In order to keep the edge of the bottom plate clean during the cutting process, the material can be heated in the range of 30-100℃.
In order to obtain a neat cut, the board must be firmly pressed down by a spring device to prevent other unavoidable displacements of the board during the cutting process. In addition, parallax can also lead to a tolerance of 0.3-0.5rnrn, which should be minimized, and the use of corner markers can improve accuracy.
The shearing machine can handle various sizes and can provide accurate repeat sizes. Large machines can cut hundreds of kilograms of substrates per hour.
Sawing
Sawing is another method of cutting PCB substrates. Although the size tolerance of this method is similar to that of shearing (0.3-0.5 rnrn), this method is more preferable because the cutting edges are very smooth and neat.
In the manufacturing process of printed circuit boards, circular sawing machines with movable worktables are mostly used. The adjustable range of the saw blade speed is 2000-6000r/rnin. But once the cutting speed is set, it cannot be changed.
The diameter of the high-speed steel blade is about 3000rnrn, and it can cut paper-made savory materials at a rate of 2000-3000r/rnin with approximately 1.2-1.5 teeth per 1cm circumference. For epoxy glass substrates, tungsten carbide blades are used. The cutting effect of the diamond wheel will be better, although it has a large investment at the beginning, because of its long service life and can improve the edge cutting effect, it is very beneficial for future work.
If the operation is improper when cutting the printed circuit board, it will affect the appearance of the printed circuit board on the one hand, and also affect its structural performance on the other hand. If you want to know more about printed circuit boards after reading the above, you can get a comprehensive solution by contacting us.
As a professional PCB product manufacturer, we have accumulated rich production and design experience in this field. We have a professional production team that manufactures in full accordance with strict standards and can provide customers with safe and high-quality products. We can also provide corresponding customized services and professional solutions according to customer needs. If you want to buy our printed circuit boards, please contact us immediately!