What Are the Different Soldering Techniques for Assembling Printed Circuit Boards?
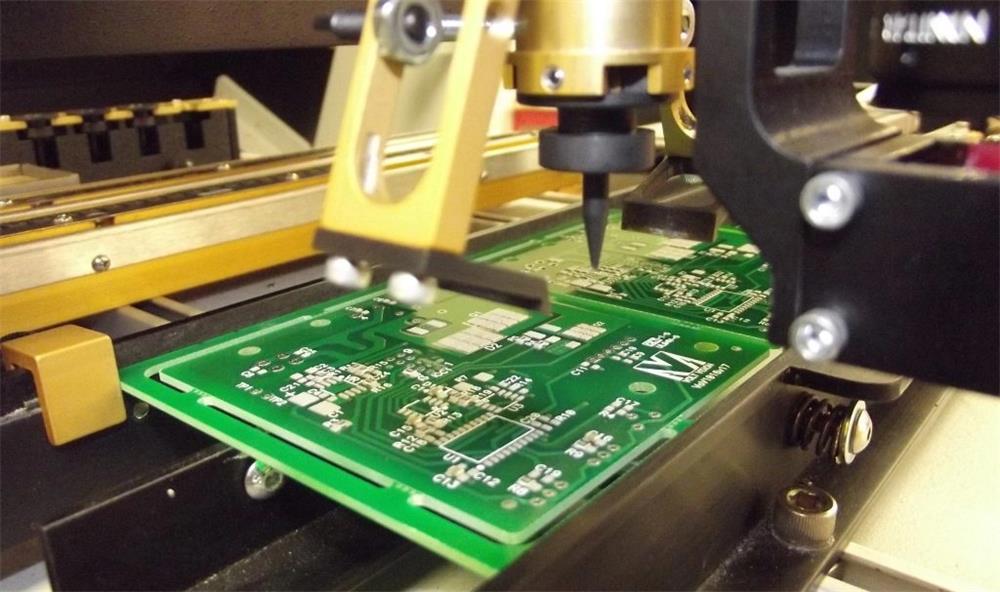
The choice of soldering technique depends on your needs, the materials used, and other specific factors such as high heat resistance or other requirements. Before choosing the right welding process, you must know the following considerations for these different welding techniques.
PCB soft soldering
Soft soldering is a popular soldering process in the PCBA assembly industry. Also the best choice for connecting smaller, compact, fragile components to printed circuit boards.
Soft soldering is a type of connection method that uses solder with a melting point of not more than 450℃ and is heated to a soldering temperature that is lower than the melting point of the base metal and higher than the melting point of the solder. The brazing filler metal spreads on the closely fitting joining surfaces by capillary action or on the workpiece surface by wetting.
Soldering material is a soldering material for soldering whose liquidus temperature (melting point) does not exceed 450℃. Solder filler metals are usually alloys that do not contain iron. A temperature of 450℃ is the demarcation point between brazing and soldering.
Most of the process parameters and influencing factors involved in brazing also apply to soldering. In fact, industry terms such as soldering, brazing, or silver soldering are also used to distinguish soldering from brazing.
Classification of soldering
1. Dip soldering
Dip Soldering (DS) is a soldering method that utilizes a heated metal bath of molten solder. Solder can be kept molten by any heat source. Solder dipping equipment is usually automated and programmed to control the pre-cleaning, fluxing, preheating, and dipping processes.
2. Furnace soldering
Furnace Soldering (FS) is a soldering method in which the workpiece to be welded is heated in a furnace. When soldering in a furnace, the weldment must be assembled and held in place. Solder must be preloaded into the joint. The furnace may be heated using any suitable fuel or energy source.
3. Induction soldering
Induction soldering (IS) is a soldering method that uses resistance heat generated by an induced current in the workpiece for heating, which is similar to induction soldering.
4. Infrared soldering
Infrared Soldering (IFS) is a soldering method that uses infrared radiant heat for heating, which is similar to infrared soldering.
5. Soldering iron soldering
Soldering Iron Soldering (INS) is a method of soldering that utilizes heat from a soldering iron. Soldering irons have a part called a heating head that heats and transfers heat to the solder, which is made of copper. The heating head of the soldering iron can be heated in different ways, for example, the electric soldering iron is heated by the internal resistance coil; there are also flame heating and furnace heating.
Soldering torches are also used in the industry, which use resistance heat and whose heater head is a high resistance element. Soldering torches are widely used in electronic component assembly. Soldering iron soldering is generally done manually.
6. Resistance soldering
Resistance soldering (RS) uses the resistance heat generated when an electric current flows through the weldment. This method is slightly different from resistance brazing, which usually requires the use of hand-held tools for welding, and requires the introduction of low voltage and high current to the weldment.
This method is commonly used in electrical equipment manufacturing. The figure below shows an example of an application of resistance soldering of lugs to soldered cables. Solder is usually added by hand. This method is also used for brazing industrial copper pipe fittings.
7. Flame soldering
Flame soldering (TS) is similar to flame soldering, except that it uses lower brazing temperatures and uses air instead of oxygen as the combustion gas. Use a small propane gas cylinder to which a torch head is attached, and the cylinder becomes a handle. Solder is added manually. Flame soldering is widely used in the pipe fitting industry to braze pipes and copper fittings.
8. Wave soldering
Wave soldering is an automated soldering method primarily used to mount electronic components on printed circuit boards. Solder by sliding the solder side of the board over the wave of molten solder. The electronic component leads are first inserted into the circuit board and secured to the printed traces on the back of the printed circuit board.
Then, the printed circuit board is placed on the groove containing the molten solder, and the printed circuit board is brought into contact with the crests of the solder, thereby soldering it to the leads of the electronic components. This is a fully automatic method and results in high quality welds. This method is widely used in the electronics industry.
PCB brazing or silver soldering
Brazing heats the melting filler (solder) with a melting point lower than the workpiece to be connected to a temperature higher than the melting point, so that it has sufficient fluidity, and fully fills between the two workpieces by capillary action (called infiltration), and after it solidifies A method of joining the two together.
Brazing has many advantages over other metal joining techniques such as welding. Because welding does not melt the joined base metal, it allows for tighter tolerances and produces clean joints without the need for secondary machining. In addition, it can weld different metallic and non-metallic materials (eg metalized ceramics).
In general, brazing also produces less thermal deformation than welding due to uniform heating. Complex and multi-component workpieces can be welded. Another advantage is that brazing can coat or wrap the base metal for protective purposes. Finally, brazing is easily adaptable to mass production and can be automated because individual process parameters are not sensitive to changes.
Brazing
Compared to soldering and brazing, brazing uses the highest temperatures and produces the strongest joints. Brazing is similar to brazing in that metal components or parts are joined by high temperatures. Soldering is different in that it melts the metal on the bottom to fit the filler metal designed for your board. Soldering is an easily automated mass production process best suited for joining two separate PCBs with less thermal distortion.
Wave soldering
Wave soldering is used for assembly in through-hole processes or surface mount technology (SMT). It is used for the mass assembly of printed circuit boards. The PCB goes over a pan of molten solder that looks similar to a wave pool (that's where the name comes from). When the board is in contact with the solder, the board components are attached together. Components must be glued to the board prior to SMT wave soldering.
The SMT method has become more popular than through-hole, making wave soldering a less popular technology choice. Wave soldering was subsequently replaced by reflow soldering.
Reflow soldering
The reflow soldering process involves the use of heated solder paste to attach components to a circuit board. The solder paste is heated and turned into a molten state, allowing the pads and pins to connect.
Materials needed to solder the PCB
While some of the materials used in fabrication and welding may vary from project to project, the following basic materials will be used in every welding process.
Soldering Iron: The soldering iron is the heat source used in the soldering process. This is a pen-shaped metal tool that allows you to manipulate solder. Components of a soldering iron include the tip, handle, solder wire eraser, and a resting place when not in use.
Solder Paste: This is a gray putty that attaches the leads of the component to the circuit board.
Flux: Flux is a chemical cleaning agent. It aids in rust removal, prevents future rust by trapping air, and makes your solder paste easier to apply by preparing the surface.
Once the wrong soldering process is selected, it is possible to directly burn the PCB or cause the finished product to fail. If you want to know more about PCB after reading the above, please continue to pay attention to our news.
PCB Quick is an experienced PCB product supplier. We have a professional production team and a comprehensive management system. We have carried out comprehensive quality control whether from PCB design, packaging, or export. Our products are also sold all over the world because of their excellent performance. If you are interested in our printed circuit boards, please contact us immediately!