What Are the Advantages of Rigid-flex PCB?
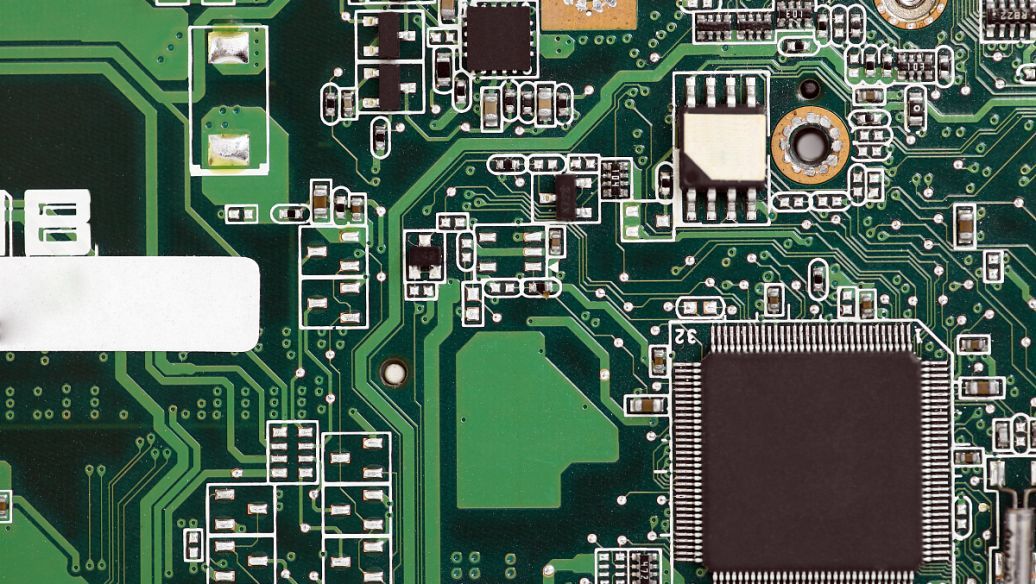
Rigid-flex PCB is a combination of rigid and flexible substrates. One or more flex circuits are used to connect subcircuits on a rigid PCB. Rigid flex PCBs are usually made of flexible polyimide material on a copper-clad substrate and attached to a rigid FR4 board.
The flex portion of a rigid-flex PCB usually has a multi-layer structure with a pad to ensure interconnection between the layers. Rigid-flex PCBs have evolved from just using flex substrates to replace wiring harnesses to building actual subcircuits on the flex area itself.
The advantages of rigid-flex PCB
Designing rigid-flex PCB is more challenging than traditional rigid PCB. However, there are good reasons to use rigid-flex in some designs, especially those involving mounting boards in tight spaces.
Improve reliability
Connectors come into play when the wiring harness needs to be periodically removed from the PCB. For designs involving multiple interconnected subcircuits in the enclosure, adding connectors to the PCB only increases the risk of failure.
Implementing a rigid-flex design eliminates the need for board-to-board connectors. This also results in fewer solder joints, which are sometimes prone to failure.
Save space
Designs that often require rigid-flex PCBs are a luxury space. Handheld thermal scanners, for example, can benefit from rigid-flex PCB designs because there isn't much room for wiring harnesses and high-profile connectors. Instead, by building interconnect circuits on a flexible substrate, you'll have more room for wiring.
Reduce costs
Rigid-flex PCBs are generally less expensive than rigid PCBs. Although the former is more difficult to produce, using a rigid-flex PCB may reduce the overall cost of the product. You'll save on assembly costs as wired interconnects are replaced by conductive layers of flexible material, which in some cases require manual labor.
Since the rigid-flex PCB is a complete circuit in itself, there is no need to install wiring harnesses in the enclosure in which it is mounted. Such wiring work takes up valuable time and is an additional cost per product unit.
Easy to test
Automated testing of rigid-flex PCB is also easy because all subcircuits are already interconnected when the PCB is fabricated. The ability to eliminate connection problems prior to the assembly of components further prevents unnecessary waste and expense.
Rigid-flex PCB design challenges
As products are in the stage of miniaturization, there is an urgent need for PCB designers who are proficient in rigid-flex design. Before taking on the challenge, it's important to realize that designing rigid-flex PCBs requires a different skill set.
Instead of taking a purely electrical approach, you need to start envisioning your designs in 3D. Rigid-flex designs are often installed in housings and mechanical elements must be considered.
Flexible parts of PCBs sometimes bend to a certain degree, which means you need to weigh the mechanical stress on the material. Bend lines or bent areas require careful handling to prevent premature failure.
Avoid using vias and pads in curved areas as mechanical stress may weaken the pads. For structural stability, the traces should also be perpendicular to the bend lines. You can add dummy traces to reinforce bend areas along with existing traces.
If you want to know more or want to buy PCB, please contact us.
PCBQuick can provide you with custom circuit board solutions. We support 24-hour online quotations and a 12-hour expedited service for PCB prototypes. Specializing in the production of single-sided PCB, double-sided PCB, multi-layer PCB, aluminum substrate, and flexible PCB; our products are widely used in high-tech fields such as communications, computer technology, industrial control, automotive, LED lighting, etc.